Студентам > Курсовые > Разработка технологического процесса сборки и монтажа печатной платы «Пульт ДУ»
Разработка технологического процесса сборки и монтажа печатной платы «Пульт ДУ»Страница: 8/13
 0,007
  0,0015
  0,0013
  0,0011
       0,0009
0,1 0,2 0,3 0,5 1 2 t1 мм | |
Рисунок - График зависимости погонной индуктивности от ширины | |
Вычисляем частоту паразитного контура. Резонансная частота контура образуемая паразитными связями определяется по формуле:
Fпар = Ö1 / С((L1 + L2) – 2М) = Ö1 /1.44*10-9 *((4.5+1)*10-2)-2*5.4*10-12 = 2.5 (мГц)
Полученная частота лежит вне диапазона в рабочих частотах проектируемого устройства, следовательно, влияние на работу устройства она не оказывает.
5 Выбор и обоснование технологического процесса сборки и монтажа печатных плат
Методы сборки и монтажа печатных плат можно классифицировать по степени автоматизации сборочного – монтажных работ. При этом можно выделить следующие методы сборки:
Ручная:
1) Ручная подготовка элементов, ручная установка элементов, ручная пайка.
Частично ручная:
2) Ручная подготовка элементов, ручная установка элементов, автоматическая пайка.
С помощью автоматического оборудования:
3) Ручная подготовка элементов, автоматизированная установка элементов, автоматическая пайка.
4) Автоматизированное производство.
Следует отметить, что первый метод используется в единичном и мелкосерийном производстве и не имеющих автоматизированных процесов. Второй в основном в мелкосерийном, в среднесерийном частично, а третий и четвертый в крупносерийном производстве и массовом.
Установку ЭРЭ производится в ручную 150-30 А2 МО 400 ООО ТУ, обрезку производить кусачками по ОСТ4.ГО.060.012. Пайку производить на установке УПВ 903Б.
При разработке технологического процесса сборки и печатной платы проектированной мною устройства предлагаю применить второй вариант, при котором подготовка и установка осуществляется вручную, а пайка осуществляется автоматизировано.
Этот вариант является наиболее эффективным и целесообразным в соответствии с применяемым оборудованием имеющим на данном обороте. Он позволяет проводить минимальные затраты.
Для пайки дефектных соединений и пайку выводов ЭРЭ, устанавливаемых после пайки волной, производить в ручную электропаяльником ЭПНЦ=25/36 ГОСТ7219-83. При разработке технологии производства сборки печатной платы предлагаю применить частично автоматизированную методику производства, при которой подготовка и установка ЭРЭ осуществляется на полу автоматах или в ручную, а пайки ведется автоматически УПВ903Б установку технологии производства подготовки ЭРЭ к монтажу, технология производства установки ЭРЭ на печатную плату, сборке блоков, пайки электрических соединений следует проводить с учетом требований изложенных в следующих ОСТ:
ОСТ4.ГО.054.263
ОСТ4.ГО.054.264
ОСТ4.ГО.054.265
ОСТ4.ГО.054.266
ОСТ4.ГО.054.267
При проектировании технологии производства сборки печатной платы, много больше учтены требования к выше изложенным документам (разрабатывая технологию печатной платы я учитывал отросливые стандарты, которые были изложены ранее).
6 Выбор технологического оборудования применяемого для сборки и монтажа печатных плат
Сборка компонентов на ПП состоит из подачи их к месту установки, ориентации выводов относительно монтажных отверстий или контактных площадок, сопряжения со сборочными элементами и фиксации в требуемом положении. Она в зависимости от характера производства может выполняться вручную, механизированным или автоматизированным способами рисунке ниже. | | 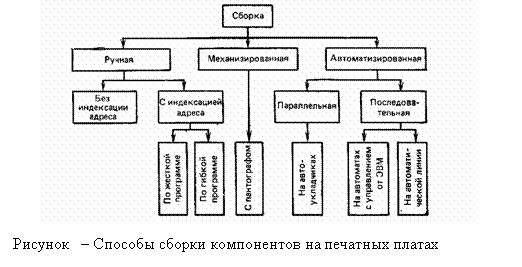 |
Применение ручной сборки экономически выгодно при производстве не более 16 тыс. плат в год партиями по 100 шт. На моей плате расположено не более 40 элементов, в том числе 2 ИС. Существенным достоинством ручной сборки является возможность постоянного визуального контроля, что позволяет использовать относительно большие допуски на размеры выводов, контактных площадок и монтажных отверстий, делает возможным обнаружение дефектов ПП и компонентов. Если число устанавливаемых компонентов составляет от 5 до 50 млн. шт. в год, целесообразно использовать автоматизированное оборудование с управлением от ЭВМ. В условиях массового выпуска однотипных ПП (0,5 .1 млн. шт. в год) применяются многостаночные линии, в которые входит до 50 единиц автоматического оборудования.
На ручную сборку компоненты целесообразно подавать подготовленными с облуженными, формованными и обрезанными выводами, уложенными по номиналам в технологические кассеты или магазины. Основная задача сборщика состоит в оперативной и правильной установке требуемого элемента на место, обусловленное конструкцией ПП. Чтобы уменьшить число ошибок, при сборке на ПП со стороны установки компонентов способом шелкографии наносятся их номер и направление установки или используется эталонная собранная плата. Кассеты и магазины элементов имеют аналогичные обозначения и располагаются вокруг места сборщика на удобном для него расстоянии. Печатные платы устанавливаются в держателе при помощи быстрозажимных фиксаторов. Повышение производительности достигается использованием многопозиционного держателя, в котором параллельно друг другу располагается несколько ПП. Рабочий за один прием устанавливает необходимое число одинаковых элементов на все платы.
|